Why 3PLs should use a WMS
Third party logistics providers (3PLs) have a strong responsibility to their clients with the goods entrusted to them in their warehouse operations. Clients expect their goods to be handled, stored, and processed on time and accurately. A particularly significant factor to note is that most 3PLs work with multiple customers, each with unique needs and requirements, all with the expectation that processes are done rapidly and efficiently.
3PLs and warehouse operations require warehouse management software (WMS) in order to effectively manage the complex make-up of warehouse operations, minimize costs, and bring transparency to information and data. A warehouse management system (WMS) consists of software and processes that allow organizations to control and administer warehouse operations from the time goods or materials enter a warehouse until they move out.
The purpose of a WMS is to help ensure that products and materials move through warehouses in the most efficient and cost-effective way. A WMS handles many functions that enable these movements, including inventory tracking, picking, receiving, and stocking. A WMS also provides visibility into an organization’s inventory at any time and location, whether in a facility or in transit.
WMS benefits
Adopting Warehouse Management Software will result in vastly improved processes and systems within a 3PL facility. Some benefits include:
- Efficient labor management
- Complete stock traceability and visibility
- Reduced number of picking errors
- Accurate inventory counts
- Remote data visibility
- Reduction in returns
- Minimized paperwork across all departments
- Improved customer service
- Automatic implementation
- Greater responsiveness
Picking the right WMS for your 3PL facility
Warehouse management software seamlessly processes data and coordinates the movements of your warehouse. Those two components are the foundation of your business, so you want to make sure that the WMS you pick meets your needs. Can it produce reports? Manage large volumes of transactions?
Key Functionality
The ideal WMS solution for third party logistics providers must be able to meet the needs of each specific client including billing, labeling, reporting, and operational processes. The best WMS for 3PL is built with the ability to service multiple customers at once.
Whether web based or on premise, a 3PL warehouse management system should include basic capabilities plus specific features for servicing a wide variety of individual customers including:
- Multiple Clients – multiple inventory owners
- Complex labeling requirements
- Inventory management and control
- Reporting tools
- Shipping and receiving functionality
- Dock door appointment scheduler
- Packing and shipping functionality
- Comprehensive warehouse management operations including cycle counts
- Integration with other software and systems
- Concurrent support for business processes of each inventory owner
- Order Entry is self-contained in the 3PL solution
- 3PL logistics WMS may need to accommodate different ERP version releases, distinguishing and accommodating the various versions automatically
Choosing a WMS Vendor
If you are operating a 3PL warehouse, then you’re looking for tips on how to pick software specifically for 3PLs, especially if you are currently relying on manual processing or outdated software systems.
Things to look for when choosing a 3PL-specific WMS:
- Scalable Functionality: You want your business to continue growing so you’ll want to pick a WMS that meets your evolving needs. You don’t want to invest and not have any room for expansion.
- Innovative Technology: Pick a WMS that you trust. You want to invest in the best technology to meet your 3PL needs, so keep your must-have functionality in mind.
- Labeling Compliance: There are regulatory requirements involved in the processing and labeling of packages. With software, you can effectively function and efficiently meet those needs.
- Billing: Operating your 3PL manually is bound to result in misplaced invoices and other problems. However, billing functions that are included with 3PL solutions help you ensure that all storage, receiving, shipping, and billing are accurate and on-time.
- Support: Getting a new system can be perplexing even to the most advanced user. So having access to effective technical support is a must.
Conclusion
When adopting new 3PL technology, remember to keep your customers’ concerns in mind. Their customer is the consumer. Making the shift from a private warehouse to a 3PL can be daunting for many businesses. They are now trusting another entity to function and manage their product, process, and consumers. As the owner of a 3PL, you must be ready to meet their needs with the latest technology to oversee all steps with ease.
Your goal is to achieve customer retention and satisfaction. The key to doing that is to make sure that the warehouse customer and the consumer are both happy by providing a solid platform for your 3PL inventory and task management strategies. A WMS is a necessary component of the entire 3PL strategy. Your technology must stay up to date to provide the best services possible and stay ahead of the competition.
CAI’s ROC Warehouse Management System operates with third party logistics providers in mind. ROC delivers near 100% inventory accuracy. This is true, not just for the quantity on hand for each inventoried item, but also the quantity on hand of each item in each location for each lot or pallet. High inventory accuracy combined with paperless order picking means very high pick accuracy — which saves significant money.
CAI’s WMS solution delivers clear views of activity and business information within warehouse operations, tailored to each of the customers’ goods you store and manage. You can view on-screen visibility to a variety of key performance indicators (KPIs) and information. Then easily share it with sales, accounting, planning, and management resources.
Learn more about ROC WMS by participating in a demo with a member of our team. Click here to schedule!
About The Author
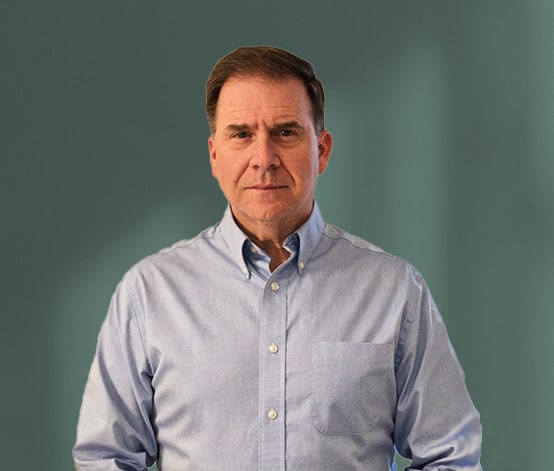