7 Benefits of Real-Time Production Monitoring in Manufacturing
Many manufacturing companies have dashboards and software systems that show data from the previous day—but how is that information helpful for making real-time decisions and maximizing performance today?
Today’s fast-paced manufacturing landscape requires real-time monitoring of business processes in order for companies to stay relevant and competitive. The challenge is that accessing real-time data from production and processing equipment can be difficult for many manufacturing companies.
Fortunately, new technologies make real-time production monitoring a reality for manufacturers, providing managers and stakeholders with the insights and information they need to make real-time data-driven decisions, optimize business operations, and improve efficiency.
What Is Real-Time Production Monitoring?
Real-time production monitoring is the process of collecting and analyzing up-to-date data from machines and employees in a manufacturing environment, providing information about systems, processes, events, and operations in real time. It allows managers and engineers to respond to issues and trends quickly, make more accurate decisions, and track key performance indicators (KPIs) such as productivity, quality, and delivery time.
What Are the Benefits of Real-Time Production Monitoring for Manufacturers?
Real-time production monitoring is a powerful tool for enhancing the efficiency and effectiveness of manufacturing processes. It can help manufacturers gain more visibility and control over the production process, standardize data and best practices across the supply chain, gain a competitive edge in the market, and reduce production downtime. Overall, real-time production monitoring is not only beneficial for safety reasons but also for improving the quality and profitability of manufacturing operations.
Manufacturers can experience significant advantages by implementing real-time production monitoring software, including the following benefits.
1. Improved Visibility & Transparency
Real-time production monitoring allows managers to access detailed and accurate data about the status and performance of machines, equipment, production lines, and employees. For example, real-time production monitoring can show how much time is spent on value-added activities vs. non-value-added activities, such as setup, maintenance, or rework. It can also reveal how different machines and employees affect overall equipment effectiveness (OEE).
This improved visibility and transparency can help manufacturers identify problems, bottlenecks, and opportunities for improvement in the manufacturing process.
2. Standardized Data & Best Practices
Manufacturers need accurate, up-to-date, and standardized data to make informed decisions, adapt to changes, and seize market opportunities. Real-time production monitoring can help managers collect and compare this data across different machines, shifts, plants, or even regions. With increased access to real-time data, they can establish better benchmarks and standards for optimal performance.
Additionally, real-time production monitoring can facilitate the sharing of best practices and knowledge across different teams and locations as well as help managers identify the most efficient methods, tools, or settings for each operation and machine.
3. Better Competitive Advantage & Increased Customer Satisfaction
In today’s crowded manufacturing market, getting an edge over the competition is vital to a manufacturer’s success. Real-time production monitoring can help managers optimize the production process and deliver high-quality products on time, which can increase the value of products to customers and enhance the reputation of the company.
Customers expect a seamless experience. Real-time production monitoring enables manufacturers to respond quickly and effectively to changing customer demands or market conditions. For example, real-time production monitoring can assist managers in adjusting production schedules, inventory levels, or resources according to customer orders or feedback.
4. Faster Incident Response & Mitigation Time
Continuous monitoring is key to faster incident response and mitigation time. When technical glitches occur in a production line or there is a breach in security, real-time production monitoring instantly alerts the relevant employees to the problem and prompts immediate action to address it.
This fast incident response time made possible by real-time monitoring makes it easier for manufacturers to respond to incidents quickly, minimizing downtime and ensuring critical issues are solved before they escalate into more significant concerns.
5. Enhanced Operational Efficiency
With its comprehensive visibility and up-to-date data interpretation, real-time production monitoring provides superior insight into various processes, workflows, and operations. Manufacturers can track a variety of KPIs, zoom in on bottlenecks, and analyze inefficiencies—providing the information they need to make targeted improvements, optimize production lines, reduce waste, and enhance overall efficiency.
6. Superior Quality Control
Manufacturers have a responsibility to ensure manufactured goods meet quality parameters and customer expectations. Real-time production monitoring plays a critical role in quality control by constantly collecting and sharing data about products as they are being manufactured, such as identifying defects, noting deviations, and checking quality criteria on an ongoing basis.
Managers and operators can use this real-time data to correct issues before they snowball or bottleneck production, helping increase overall customer satisfaction and loyalty.
7. Proactive Maintenance
Production lines and manufacturing operations rely on machines running smoothly and equipment operating as expected. If machines or equipment break down, it can lead to unplanned—and costly—downtime. Real-time production monitoring allows manufacturers to continuously monitor the health and performance of machinery, equipment, and production assets as well as analyze performance data to schedule proactive maintenance, which is vital to prevent breakdowns and keep operations running.
Real-Time Production Monitoring Software & Technology
Real-time production monitoring requires the use of advanced technologies, such as sensors, cameras, RFID tags, and other devices. These technologies can collect and transmit data from machines and employees in real time. They can also analyze the data and provide insights or recommendations for improvement. For example, real-time production monitoring software technology can detect anomalies or patterns in the data that might indicate potential failures or defects and suggest optimal solutions to prevent or resolve those issues.
Manufacturing companies can take full advantage of the benefits of real-time production monitoring by implementing an enterprise resource planning (ERP) solution or warehouse that meets their unique business needs.
Experience the Benefits of Real-Time Production Monitoring with CAI Software
At CAI, we create innovative, production-oriented software to help our customers across a variety of industries streamline business processes and optimize their manufacturing, processing, or distribution environment. Our goal is to provide you with industry-leading solutions that improve your business operations, all with excellent service and support.
Whether you are looking to automate production, increase your return on investment, reduce costs, or streamline operations, we can help. With our suite of tools and access to our expert team, optimizing your business processes is easier than ever.
Contact us today for a free consultation.
About The Author
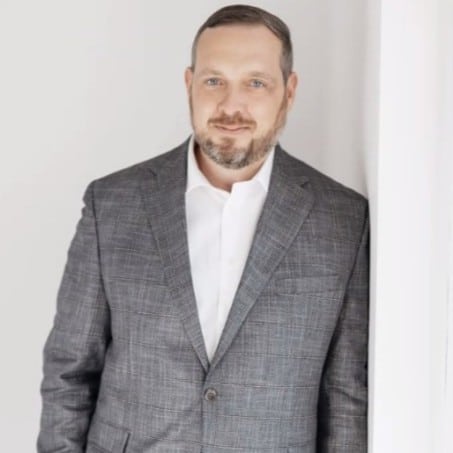