Manufacturing Machinery and Predictive Maintenance
Predictive maintenance techniques are designed to help determine the condition of in-service equipment in order to estimate when maintenance should be performed.
This approach promises cost savings over routine or time-based preventive maintenance because tasks are performed only when warranted.
Predictive Maintenance accelerates operational excellence by catching shortcomings early and proactively analyzing symptoms that may subsequently cause more defects. It helps manufacturers regulate the machine’s life, physical conditions, and work efficiency.
As stated by IoT for All, “The benefits of predictive maintenance translate to significant cost savings and increased revenue for manufacturing. Nevertheless, predictive maintenance is still not widely deployed, given that getting access to timely and detailed information about the assets’ condition is quite challenging.”
Compared to the conventional reactive and preventive models, which only gave manufacturers three options (1. Run until a failure, 2. Schedule maintenance, 3. Make a guess at intervention that could have prevented the failure), predictive maintenance offers more.
Benefits of Predictive Maintenance
- Improved OEE
- Avoidance of unscheduled downtime
- Optimal planning of maintenance activities
Get Started with Predictive Maintenance
ShopVue’s Direct Machine Interface (DMI) can help. ShopVue captures machine data automatically through an electronic interface to the machine’s controls. At frequent intervals, ShopVue polls the machines and captures key data in a machine journal. The DMI engine then processes the journal, updates ShopVue with relevant information, such as status, yield and quality records, temperature, humidity, pressure, flow rates, and RPMs.
The DMI data can be used to alert the right personnel through dashboards, Andon lights, and email alerts if an issue arises. By utilizing OPC technology and both integrated and external machine interface methods, ShopVue DMI can connect to virtually any factory machine.
Predictive maintenance catches shortcomings early before it causes stalled production, quality defects, and missed delivery dates. Real-time machine data collection guarantees accuracy in these critical metrics, and data accuracy translates to a stronger business.
About The Author
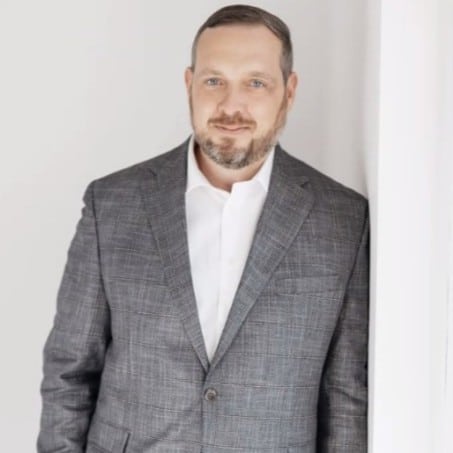