Leveraging Manufacturing Execution System (MES) Software for Labor Management
Leveraging Manufacturing Execution System (MES) Software for Labor Management One of the most powerful capabilities of a comprehensive manufacturing execution system (MES) is labor management. Built to increase production efficiency and accurately track how employees are spending their time, MES labor tracking functions allow manufacturers to seamlessly measure floor activity in real-time and help meet productivity targets.
In this post, we’ll explore what labor management is, why it matters, how an MES can support these efforts, and why your manufacturing operation needs an MES with these capabilities.
What Is Labor Management?
Labor management is all about optimizing the use of your workforce during production shifts. It encompasses a variety of activities, including the following:
- Employee scheduling: Ensuring the right people are available when needed.
- Attendance tracking: Keeping an eye on employee hours and absences.
- Performance measurement: Analyzing productivity to identify areas for improvement.
- Resource allocation: Assigning tasks based on skills and qualifications to streamline workflow.
At its core, effective labor management aims to utilize your team’s talents efficiently, maximizing output while minimizing waste.
5 Reasons Why Labor Management Is Essential for Manufacturers
Labor management is integral to the manufacturing process for several reasons.
Boosting Efficiency
Effective labor management simplifies operations on the shop floor. With the ability to start and finish production runs with minimal input—often just a quick scan of a barcode—you can streamline processes and increase throughput. This process not only helps your team focus on their tasks but also enhances overall efficiency.
Ensuring Accurate Data Collection
Real-time tracking is a cornerstone of effective labor management. It allows you to capture production metrics instantly, including quantities produced and scrap rates. By minimizing data entry errors, you ensure your reports reflect accurate, up-to-date information, which is vital for making informed decisions and optimizing processes.
Monitoring & Improving Performance
Keeping tabs on employee performance is key to identifying inefficiencies. Analyzing how team members spend their time helps you spot patterns that may be holding back productivity. If certain tasks consistently take longer than expected, you can step in with targeted support, whether that’s additional training or workflow adjustments.
Providing Comprehensive Reporting for Strategic Planning
Advanced labor management capabilities generate insightful reports on various metrics, including employee performance and production times. This historical data is invaluable for planning, allowing you to set realistic productivity targets and allocate resources effectively for future needs.
Ensuring Regulatory Compliance
In industries that must adhere to labor laws, effective labor management helps you stay compliant. Accurate tracking of employee hours, overtime, and breaks can prevent potential legal issues and penalties, giving you peace of mind.
How an MES Helps Manufacturers with Labor Management
A manufacturing execution system serves as the link between enterprise-level planning and real-time production processes. Here’s how an MES can support your labor management efforts.
Enabling Real-Time Data Tracking
An MES continuously monitors production activities, offering real-time insights into employee performance and workflow. This capability allows you to respond quickly to changing needs, reallocating labor resources as necessary. For example, if one production line is lagging, you can quickly assign extra personnel to help catch up.
Optimizing Resource Allocation
With insights from your MES, you can make informed decisions about resource allocation. The system provides data on employee skills, availability, and workload, enabling you to assign tasks based on these factors. This reallocation of resources ensures that your team is working on tasks that match their strengths—optimizing both productivity and employee satisfaction.
Automating Labor Management Processes
Many labor management tasks can be automated through an MES, reducing the administrative burden on your team. The system can automatically track employee attendance, calculate hours worked, and generate performance reports. Automating these tasks frees up valuable time for managers to focus on strategic initiatives rather than getting bogged down in manual processes.
Identifying Bottlenecks for Continuous Improvement
By analyzing production data, your MES can help pinpoint bottlenecks in the workflow. This insight allows you to identify areas that need improvement and implement changes to enhance efficiency. For example, if a specific machine is causing delays, you can schedule maintenance or adjust resource allocation to mitigate its impact on production.
Fostering Employee Engagement and Accountability
A robust MES encourages a culture of accountability by providing employees with visibility into their performance metrics. When team members can track their productivity and see how their efforts contribute to overall goals, they feel empowered and motivated. This engagement can lead to improved morale and enhanced performance on the shop floor.
Example of MES Labor Management Software in Action: Automotive Parts Manufacturer
Let’s bring labor management to life with an example of a mid-sized automotive parts manufacturer that integrates an MES with advanced labor management functionalities.
Implementation
Once the MES is in place, the manufacturer begins to track each employee’s activities in real-time. When a production run starts, operators simply scan a barcode associated with the order. The MES automatically assigns the right personnel based on their skills and availability.
Real-Time Monitoring
As production moves forward, the MES tracks performance metrics, including time spent on tasks and output rates. If a machine experiences downtime, the system alerts management, allowing them to quickly reassign personnel to other tasks or lines to maintain production flow.
Data-Driven Decision-Making
After a production run is completed, operators input the quantities produced and any scrap generated into the MES. The system flags discrepancies, prompting managers to investigate further. Over time, the manufacturer notices trends in performance data that highlight areas for improvement, such as higher scrap rates on certain lines.
Strategic Interventions
Equipped with this information, management implements targeted interventions. They offer additional training for operators on specific machines that show higher scrap rates and adjust workflows to better align with employee strengths. Over the following months, the manufacturer sees a significant reduction in scrap rates and an increase in overall productivity.
Comprehensive Reporting for Future Planning
The MES generates comprehensive reports on labor performance, allowing management to identify patterns and set realistic productivity targets for future production runs. By analyzing historical data, they can forecast labor needs more accurately, ensuring that they have the right number of personnel available to meet demand without overstaffing.
Key Takeaways & Benefits of MES Labor Management Software
Integrating labor management capabilities within a manufacturing execution system isn’t just a technical upgrade—it’s a strategic advantage that can significantly enhance your organization’s performance. To summarize, here are the key benefits of MES labor management software for manufacturers:
- Increased efficiency: Streamlined processes lead to faster production cycles and reduced downtime.
- Data accuracy: Real-time tracking minimizes errors and enhances reporting accuracy.
- Performance insights: Continuous monitoring provides actionable insights for improvement.
- Strategic resource allocation: Data-driven decisions ensure optimal personnel assignments and cost savings.
- Engaged workforce: Visibility into performance metrics fosters accountability and boosts employee morale.
Frequently Asked Questions
What Is the Significance of Labor Management?
Labor management is important because it optimizes the use of human resources in manufacturing, enhancing efficiency, reducing operational costs, and improving overall productivity.
How Does a Labor Management System Work?
A labor management system tracks employee schedules, activities, and performance metrics in real-time. It automates data collection, monitors attendance, and provides analytics to optimize workforce allocation.
How Does MES Software Help Manufacturers with Labor Management?
MES supports manufacturers by providing real-time data on employee activities, facilitating efficient resource allocation, automating labor management tasks, and offering comprehensive reporting for informed decision-making.
Why Do Manufacturers Need an MES with Labor Management Capabilities?
Manufacturers benefit from an MES with labor management capabilities to enhance productivity, reduce inefficiencies, streamline operations, and ultimately improve profitability in a competitive market.
What Is an Example of the Labor Management Function of a Manufacturing Execution System?
An example of the labor management capabilities of an MES is a system that allows operators to start and finish production runs by scanning barcodes, automatically records production quantities and scrap, and generates performance reports that help management identify trends and improve processes.
Shop Industry-Leading MES Solutions with Labor Management Capabilities at CAI Software
For manufacturers, effective labor management is more than just a necessity—it’s a strategic advantage that can lead to significant improvements in productivity and efficiency. By embracing the capabilities of a manufacturing execution system, your manufacturing operation can enhance labor management processes, resulting in smoother operations, reduced costs, and a stronger competitive edge. At CAI, we create innovative, production-oriented software to help our customers across a variety of industries streamline business processes and optimize their manufacturing environment. Our goal is to provide you with industry-leading solutions that improve your daily operations, all with excellent service and support.
Whether you are looking to automate production, increase your return on investment, reduce costs, or streamline operations, we can help. With our MES applications and access to our expert team, optimizing your manufacturing processes is easier than ever. Contact us today for a free consultation.
About The Author
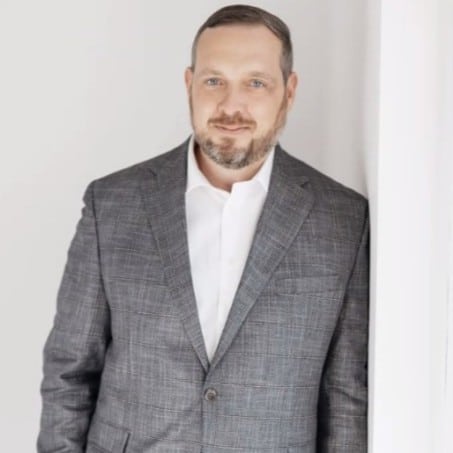