MES Buyer’s Guide: How to Choose the Best Manufacturing Execution System
The right manufacturing execution system (MES) can modernize, transform, and streamline your manufacturing organization. MES is foundational in supporting your digital transformation strategy. This software will act as the connection between your enterprise resource planning (ERP) software and the factory floor, provide real-time visibility into the entire production process, and optimize performance across production lines. What’s not to like?
Of course, the key here is the “right” MES—one that meets the unique needs of your manufacturing environment today and will continue to support you in your ongoing continuous improvement journey. That’s why selecting MES software is a critical decision for any operation.
Let’s talk about how to get things right on the first try.
How to Find the Best Manufacturing Execution System: 5 Steps to Follow
Selecting an MES is an important choice that will impact your manufacturing operations for years to come—so don’t jump headfirst into making a decision without following these steps and taking the time to research your options.
Your goal? To find the MES software that best aligns with your manufacturing operation and business objectives.
Step 1: Define Your MES Requirements
Start your search by identifying your organization’s requirements for a new MES. Do a deep dive into your existing manufacturing processes and workflows, looking for bottlenecks and inefficiencies. Find areas that need improvement, such as quality control or inventory management.
And don’t take this journey alone! Collaborate with relevant stakeholders in addition to the operations team—from IT personnel to manufacturing engineering and maintenance staff to machine operators and quality control to finance and HR teams—to get the full picture.
By figuring out your needs, you can create a detailed list of requirements to share with prospective MES vendors to help make sure you find a solution that checks off all your boxes.
Step 2: Conduct Comprehensive Vendor Research
With your requirements in mind, conduct comprehensive research on MES software vendors and their products. Every vendor has different offerings, so focus your search on vendors with experience in your specific industry that also have a track record of successful implementations.
Now is the time to examine case studies and look at testimonials. You want to get a solid understanding of potential vendors before moving forward.
Step 3: Create a Shortlist of MES Vendors
Keep narrowing down your list of potential MES vendors. Cross off any that cannot meet the requirements you defined in Step 1 and remove MES vendors that don’t serve your industry. Continue this process until you end up with three to four strong candidates
Step 4: Request Software Demos, Pricing Details, & Proposals
Contact each of the MES vendors on your shortlist. Schedule software demos to see the MES in action, get comprehensive pricing details (both upfront and ongoing costs), and request a detailed proposal. After viewing the demos and receiving proposals and pricing structures, you can easily compare MES solutions side-by-side.
Step 5: Check References & Go on Site Visits
The final step—before seeking approval from leadership and signing on the dotted line—is to perform one last check of the MES vendor’s trustworthiness and reputation. The best way to approach this process is through references.
Reach out to the vendor’s existing clients and ask about their experience with the vendor and the MES software itself. (The vendor should be willing to share a list of references with you, but you can also do some digging and talk to organizations off-list.) If possible, see if they would be open to having you stop by for a site visit to see the MES software in action.
Finally, after you’ve done your due diligence, you can begin the MES implementation process with your chosen solution.
11 Things to Consider When Choosing MES Software
To make sure your organization chooses the right MES, consider the following key factors while making your decision.
1. Hosting Model
MES solutions are often hosted in the cloud, but there are also on-premises as well as hybrid options. Each hosting model has its own pros and cons. It’s an important consideration for your final MES software decision.
2. Implementation Process
The MES implementation process looks different for every manufacturing company, even with identical products. Ask the MES vendor about their expectations for implementing the MES. How long will the process take? How much will it disrupt regular operations? Will the rollout be easy?
3. Total Cost of Ownership
How much will the MES system cost? You need an outline of the total cost of ownership. Expect more than the price of the software license itself. Expenses like hosting, customizations, user training, implementation, and ongoing maintenance are also part of the overall cost.
4. Compliance & Security
Many industries have strict regulatory requirements—and manufacturing organizations across all industries should be concerned with data security. Ensure the MES software complies with relevant standards and has robust security measures in place.
5. Training
Your employees will need to be trained to use the new MES software. What training is provided by the vendor? How long will it take to onboard your workers?
6. Support
Consider the level of ongoing support the MES vendor will provide, both during and after the MES implementation process. Additionally, think about whether you need (or will eventually) need access to support in multiple languages.
7. Data Analytics & Reporting
The best MES software provides comprehensive data analytics, gathers insights, and creates reports to help interpret results. Is the reporting dashboard intuitive? Does it display the information you need? These are important considerations for stakeholders.
8. Mobile Capability
It’s a mobile world. Is the new MES up for the challenge? An MES with mobile capabilities will allow floor supervisors, project managers, and machine operators to monitor and manage the production line from anywhere.
9. Integration Capability
What ERP system does your organization use? Will the MES be able to integrate with it—seamlessly? Make sure the MES solution can communicate with your ERP as well as other relevant manufacturing software.
10. Scalability & Flexibility
As your manufacturing organization grows and expands, your MES needs to be able to keep up. Look for MES software that can scale with your business and is flexible enough to meet your changing needs.
11. User-Friendliness
The MES software should be intuitive and user-friendly from the very beginning. In order to get employee buy-in and get the most out of the software, it needs to be as easy as possible for them to navigate.
Shop for the Best MES at CAI Software
At CAI, we create innovative, production-oriented software to help our customers across a variety of industries streamline business processes and optimize their manufacturing environment. Our goal is to provide you with industry-leading solutions that improve your daily operations, all with excellent service and support.
Whether you are looking to automate production, increase your return on investment, reduce costs, or streamline operations, we can help. With our MES applications and access to our expert team, optimizing your manufacturing processes is easier than ever.
Contact us today for a free consultation.
About The Author
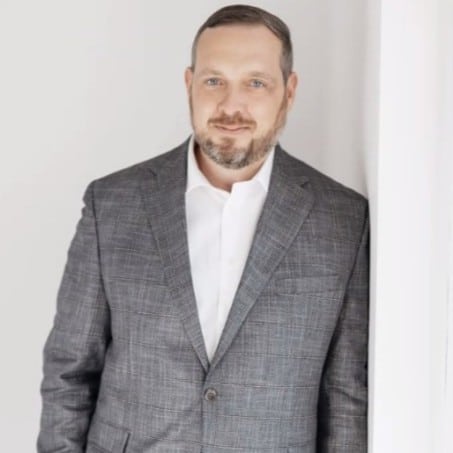