Choosing the Right Types of Manufacturing Workflow Management Software Tools for Your Business
From barcoding to serial number tracking, there’s no shortage of software solutions available to help manufacturers make the most out of their operations. Although many of these quality-of-life improvements can seamlessly transform any manufacturer into a top-flight organization, those tasked with improving existing workflows through automation, intelligent software integrations, and paperless solutions might not know where to begin when embarking on the journey towards a smart manufacturing operation.
What Is Manufacturing Workflow Management Software?
Manufacturing workflow management software refers to digital tools that are designed to help manufacturers optimize, automate, and monitor their production processes from start to finish. Whether it’s tracking raw materials, managing tasks on the factory floor, or ensuring finished goods reach customers on time, manufacturing workflow software connects the dots across departments, systems, and teams.
By replacing manual processes with real-time digital workflows, manufacturers can improve efficiency, reduce errors, and gain greater visibility into every stage of production. These tools are especially useful for identifying bottlenecks, eliminating redundancies, and ensuring that resources—whether people, machines, or materials—are used effectively across the operation.
5 Key Benefits of Manufacturing Workflow Management Software
Implementing manufacturing workflow management software brings significant improvements to operations by streamlining processes, enhancing visibility, and reducing inefficiencies. Here are five key benefits manufacturers can expect:
1. Greater Process Visibility
Workflow management software provides a real-time view of production progress, inventory levels, job status, and resource allocation. This visibility helps managers identify issues quickly, monitor key performance indicators (KPIs), and make informed decisions that keep operations on track.
2. Improved Production Efficiency
By automating repetitive tasks and optimizing workflows, manufacturers can significantly reduce downtime and eliminate unnecessary steps in the production cycle. This results in faster turnaround times and increased throughput without sacrificing quality.
3. Enhanced Quality Control
These tools help enforce standardized procedures and track quality checks throughout the manufacturing process. If defects or deviations occur, they can be flagged and addressed immediately, helping reduce waste and ensure consistent product standards.
4. Better Collaboration & Communication
Workflow management software connects teams across departments by centralizing data and updates. With everyone working from the same system, miscommunication is minimized and collaboration becomes easier, especially between the shop floor, warehouse, and office teams.
5. Reduced Operational Costs
With improved planning, reduced errors, and more efficient resource use, manufacturers can cut costs across labor, materials, and equipment maintenance. Over time, these savings can make a significant impact on profitability and scalability, allowing organizations to better allocate resources for growth.
Types of Manufacturing Workflow Management Software
Let’s take a look at how to maximize the impact of MES, WMS, ERP, inventory management, traceability, and EDI software for manufacturing to suit your specific needs:
Manufacturing Execution System (MES) Software: Smart Manufacturing
Comprehensive MES software gives manufacturers the ability to take greater control over their factory floor. From labor management to product quality, the right MES can help organizations oversee every action that impacts the creation of goods, making it easy to tweak outputs and improve productivity.
An MES helps managers address a wide range of manufacturing challenges. It adds value to a business in many ways, including:
- Easing management of raw materials
- Expanding scheduling capabilities
- Improving quality assurance processes
- Boosting throughput and uptime
- Reducing labor costs
- Improving machine utilization
- Providing real-time production metrics and data insights
Warehouse Management System (WMS) Software: Warehouse Automation
In a fast-moving, logistically complex warehouse, each inch of space and every second counts. Not only can WMS software help manufacturers streamline common distribution center tasks, but powerful automation features can also greatly improve processes related to inventory management, task management, and order fulfillment.
A WMS improves a manufacturer’s inventory management by optimizing the use of floor space, easing material rotation, and increasing inventory visibility. It enhances task management by assessing skill levels, equipment, and tasks to optimize the task assignments. It also boosts labor utilization by using labor forecasting to assign tasks beforehand and by assigning tasks in real-time to the best-suited employees. Finally, a WMS improves order fulfillment by incorporating scanners, sensors, and barcoding to improve picking and packing tasks. This capability reduces bottlenecks, and it streamlines and speeds up shipping.
Enterprise Resource Planning (ERP) Software: Connected Operations
ERP software serves as the central hub for managing a manufacturer’s business-wide operations—from accounting and finance to purchasing, production planning, and customer relationship management. By connecting departments across a unified platform, an ERP system ensures that data flows seamlessly throughout the organization.
Implementing an ERP solution helps eliminate silos, improve forecasting, streamline processes, and reduce errors caused by outdated or duplicate data. For manufacturers, ERP software is critical for managing bills of materials (BOMs), tracking work orders, and aligning supply with demand. With real-time access to key business insights, leaders can make smarter, faster decisions to drive performance across every part of the operation.
Inventory Management Software: Real-Time Inventory Control
Inventory management software gives manufacturers the tools to track inventory levels, manage stock across multiple locations, and prevent issues like overstocking or stockouts. These solutions provide up-to-date visibility into raw materials, work-in-progress items, and finished goods, ensuring that inventory is always accurate and aligned with production needs.
With features like automated reorder points, lot tracking, and inventory forecasting, manufacturers can better control material flow, minimize waste, and respond quickly to shifting demand. Inventory management software plays a vital role in supporting lean operations, reducing carrying costs, and maintaining production continuity.
Process Automation Software: Streamlined Workflows
Process automation software helps manufacturers reduce manual work by automating routine and repetitive tasks throughout the production cycle. Whether it’s triggering a quality check when a product reaches a certain stage or automatically generating a purchase order when stock levels fall below a threshold, automation ensures that critical workflows are executed with speed and accuracy.
These tools improve consistency, reduce the risk of human error, and free up valuable time for workers to focus on higher-value activities. From the shop floor to the back office, process automation plays a crucial role in increasing throughput, improving compliance, and enabling agile responses to changing conditions on the production line or in the supply chain.
Traceability Software: Supply Chain Visibility
Many industries, like food manufacturing, have strict requirements on how goods are produced and distributed. Traceability software gives manufacturers the tools necessary to track, scan, label, and analyze raw materials and finished goods as they move throughout the supply chain. Whether used to comply with audits and product safety recalls or simply add an increased layer of visibility into the manufacturing workflow, traceability gives organizations greater insight into how specific products are being crafted.
Electronic Data Interchange (EDI) Software: Paperless Workplace
For decades, EDI software has provided manufacturers with a powerful platform through which information can be readily exchanged. Able to replace email, phone calls, and other paper-based workflows, incorporating EDI solutions can empower manufacturers to weed out manual and repetitive tasks, streamline communications, and boost overall efficiency.
Manufacturers use EDI to exchange a wide variety of documents, depending on their operations. Basic documents include purchase orders (contains items ordered and pricing), functional acknowledgment (confirms the manufacturer’s receipt of the purchase order, enabling customers to resubmit a purchase order immediately if it was not received), purchase order acknowledgment (confirms the contents of the purchase order and acceptance of the order for fulfillment), and advanced shipping notice (notifies a customer that the order is being shipped, details the contents of the packages, and provides tracking numbers).
Choosing the Right Manufacturing Workflow Management Software
Depending on your circumstance, any or all of these solutions may make the difference in transforming your manufacturing workflows into an intelligent, efficient operation. CAI Software provides a variety of manufacturing solutions that can work individually or together to help you optimize operations, streamline processes, and improve your manufacturing across all areas. Whether your require better accounting functionality and centralized solutions from an ERP, better traceability and quality control to meet industry requirements from a specialized solution, better data and machine management of shop floor operations from an MES, the ability to exchange documents more efficiently through EDI, or some combination of multiple systems for more cohesive manufacturing operations, we’ve got the solution for you. For more information on how CAI’s manufacturing solutions can transform your factory and warehouse operations, check out our full line of solutions and contact us today to learn more.
About The Author
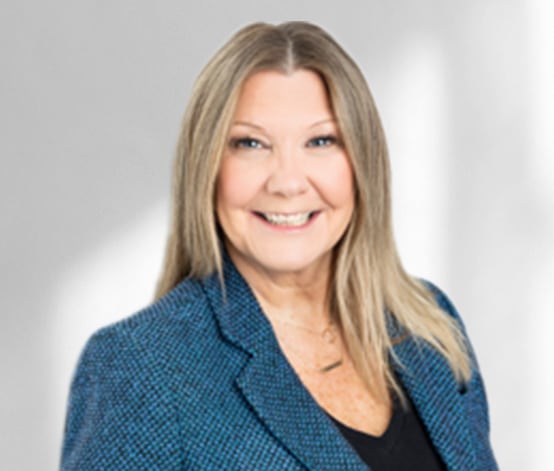